GAO Highlights of GAO-20-116, a report to congressional committees
Source: www.gao.gov/products/gao-20-116
Date: January 2020
Preface:
. . . DOD is experiencing benefits and taking steps to mitigate challenges with implementing best practices and lessons learned among the depots. Depots reported that implementing some best practices and lessons learned has led to benefits, including time and cost savings. For example, Navy Fleet Readiness Center Southwest, California, implemented an intermittent fault detection system from Ogden Air Logistics Complex, Utah, on its F/A-18 aircraft generators. According to officials, the depot reduced repair time from 90 days to 30 days and quadrupled the generators’ time between failures. . . .
Page 20-21:
Inter-service collaboration. . . . example, the Navy’s Fleet Readiness Center Southwest implemented a best practice learned from Ogden Air Logistic Complex to improve testing of electrical circuits. Specifically, according to depot officials, a maintainer at Ogden created a method—Intermittent Fault Detection and Isolation System—which tests systems and software to detect, isolate, and repair intermittent problems due to open circuits, short circuits, and poor wiring by replicating the environment of the aircraft in flight (See fig. 8.). According to Ogden officials and program documentation, by implementing this best practice, they have recovered out-of-service assets and generated about $62 million in cost savings. For example, after testing its F-16 chassis, Ogden officials recovered 138 out-of-service assets—amounting to $42 million of flight hardware returning to service.
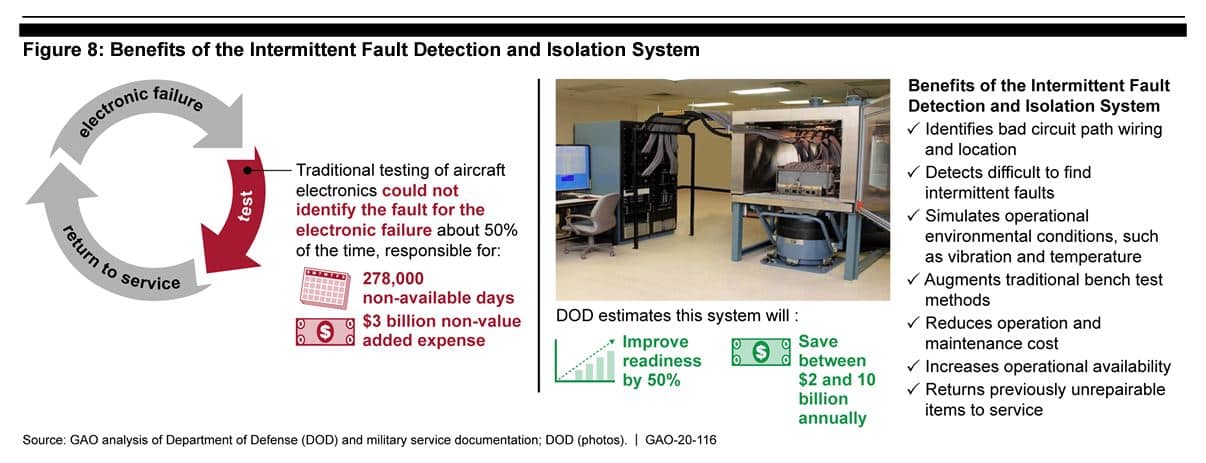
Figure 8: Benefits of the Intermittent Fault Detection & Isolation System (IFDIS)
Moreover, officials at Fleet Readiness Center Southwest visited Ogden during a benchmarking trip to discuss the process of implementing the Intermittent Fault Detection and Isolation System to test their systems. According to officials from the Office of the Secretary of Defense, the intermittent faults due to aircraft electrical systems amounted to more than $300 million in operating and support costs in fiscal year 2014. The Fleet Readiness Center Southwest used the Intermittent Fault Detection and Isolation System to test its F/A-18 aircraft generators, which provide electrical power to the aircraft. As a result of testing these generators using the Intermittent Fault Detection and Isolation System, the mean time between failures for the generators has increased, according to officials, from 104 flight hours to over 400 flight hours, and the Navy anticipates a reduction of about 30 to 90 days of repair time.
Page 26-27:
Approval process. . . . time-sensitive engineering decisions for one of its new weapon system reside at another location, which has caused delays in making timely decisions. In another example, depot officials told us that they had to get approval from individual program managers to implement the cold spray technology and the Intermittent Fault Detection Isolation System.
. . . Finally, the Office of the Assistant Secretary of Defense is providing specific guidance in implementing best practices and lessons learned, such as the memorandum issued in April 2019 on the Intermittent Fault Detection and Isolation System directing the military services to adopt this best practice.