The Wright Brothers
of No Fault Found
Awards
Prognostic Solutions
Universal Synaptics advanced intermittence diagnostic solutions employ patented neural-sensing circuitry that monitors all potential failure points individually, yet simultaneously, in parallel.
Our all-lines-all-the-time capability guarantees measurement of the right circuit at the right time, never missing an intermittent event in compliance with US Department of Defense (DoD) MIL-PRF-32516 for electronic test equipment, intermittent fault detection and isolation for chassis and backplane conductive paths.
Intermittent Fault Detection And Isolation System 2.0™ (IFDIS 2.0™)
The IFDIS 2.0 is capable of interfacing in increments of 1,280 electrical connection points. IFDIS 2.0 is a patented diagnostic instrument that can simultaneously and continuously monitor all unit under test (UUT) circuits, individually at the same time, detecting intermittent faults that occur, even as short as *50 nanoseconds (0.00000005 seconds) in duration.
Intermittent Fault Detector™ (IFD™)
The portable IFD is capable of interfacing with 128, 256, or 512 electrical connection points. The portable IFD is a patented diagnostic instrument that can simultaneously and continuously monitor all unit under test (UUT) circuits, individually at the same time, detecting intermittent faults that occur, even as short as *50 nanoseconds (0.00000005 seconds) in duration.
And Events
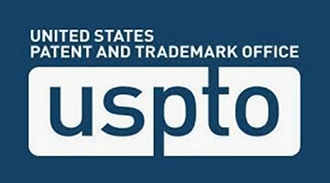
Universal Synaptics Awarded Additional Patent Protection from the USPTO
22 August 2022
Universal Synaptics announced today the notification from the United States Patent and Trademark Office of the issuance of US Patent No. 11415639…
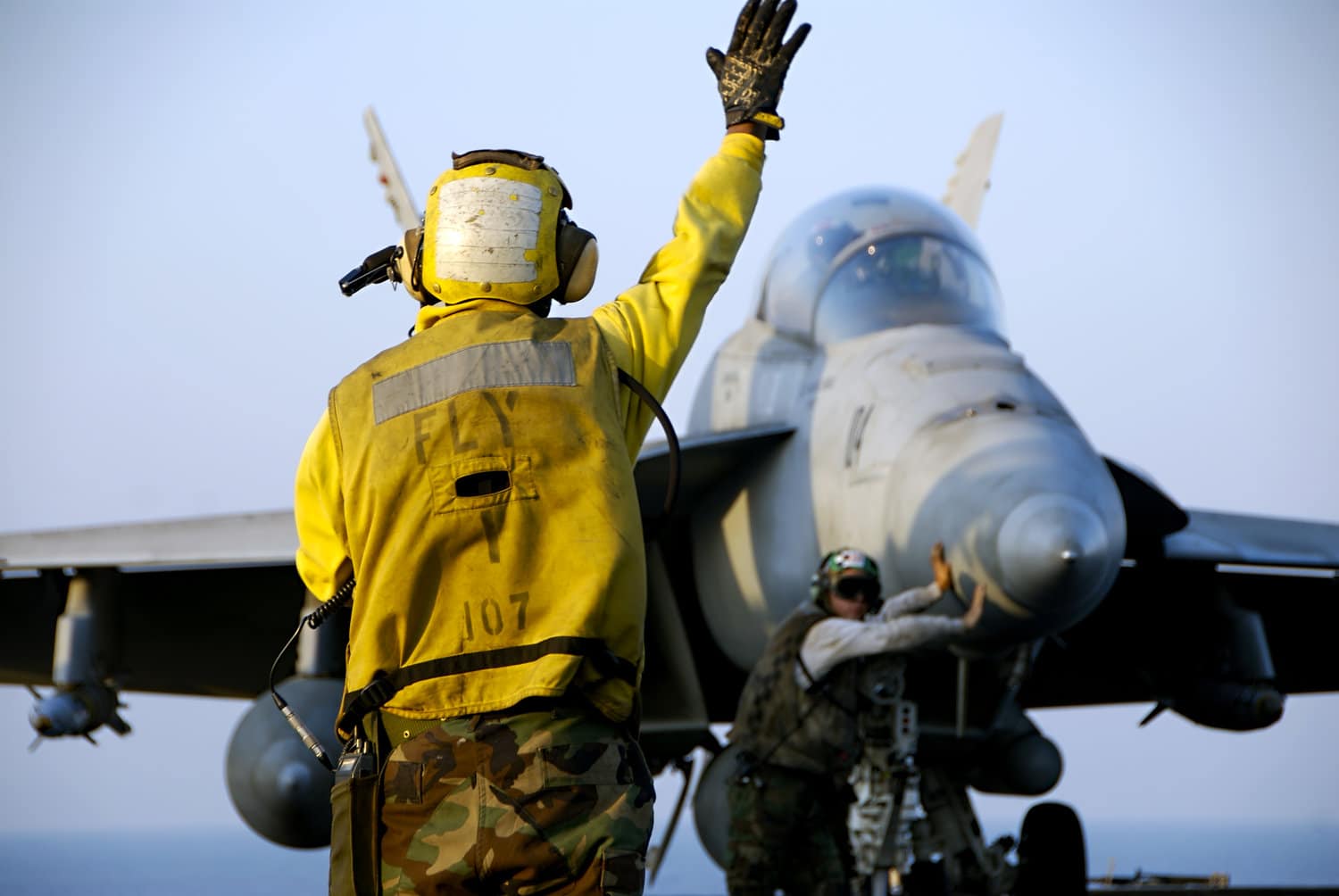
FRCSW Generators Shop Serves Multiple Naval Airframes – IFDIS
19 August 2022
Universal Synaptics’ Intermittent Fault Detection (IFD) technology was recently featured in an article entitled FRCSW Generators Shop Serves Multiple Naval Airframes, published on August 12, 2022 by Fleet Readiness Center Southwest (FRCSW).
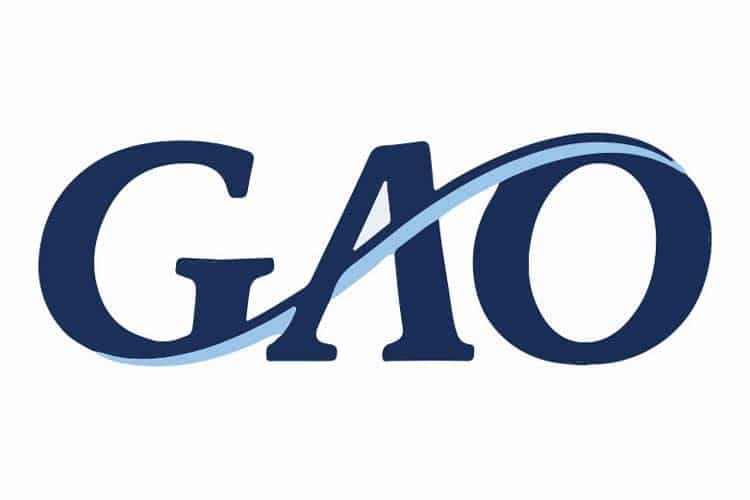
GAO-20-116 Report IFDIS Highlights – MILITARY DEPOTS Can Benefit from Further Sharing of Best Practices and Lessons Learned
9 August 2022
. . . DOD is experiencing benefits and taking steps to mitigate challenges with implementing best practices and lessons learned among the depots…
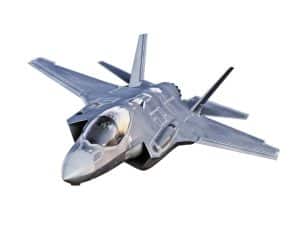
Universal Synaptics Portable Intermittent Fault Detector™ Achieves F-35 Joint Program Office Authority to Operate
2 February 2021
Universal Synaptics announced today that the F-35 Joint Program…
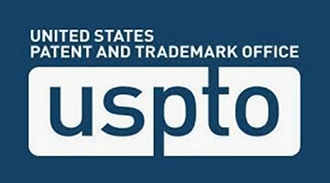
Universal Synaptics Awarded Another Patent for Intermittent Fault Detection (IFD) and Isolation from the USPTO
17 April 2020
Universal Synaptics announced today the notification from the United States Patent and Trademark Office of the issuance of US Patent No. 10,641,826“Method and System for…
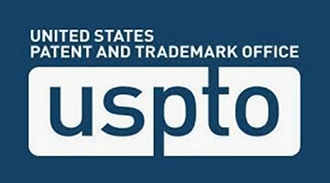
Universal Synaptics Releases Synapse
20 April 2020
Universal Synaptics announced today the release of Synapse™, a new Intermittent Fault Detection & Isolation application which maximizes usability and provides…
dedicated to reducing life-cycle costs and improving materiel readiness through reducing No Fault Found.